Additional Harwood Flooring Costs to Be Aware Of
Hardwood Floor Additional, Optional, and Behind the Scenes Costs
A plurality of factors can affect the cost of installing hardwood floors. While the total size and location of the installation (indoors, outdoors, etc.) all influence the price, there are additional details behind the scene that you should know when calculating the cost of installing new hardwood floors. Here are the 10 most expensive elements behind the scenes that affect the cost of hardwood floor installation per square foot:
- Evening the Floor: If the subfloor is uneven, then leveling must take place prior to installing the new hardwood floor. Estimating the cost is based on the time it will take to level the floor. The hourly cost ranges from $80.00 to $150.00 per hour, depending on the amount of people needed to level the floor. One man might do the job in 8 hours, while sometimes two men can finish the job in a single day. On average, such work costs around $600.00 to $700.00 for 120 square feet. Each leveling project has its own needs, making consulting with contractors highly recommended. In most cases, contractors will figure out how you can save money on leveling the floor using the quickest and easiest method.
- Staircase Costs: Hardwood stair installation costs range from $100.00 to $200.00 per step. Take into account labor, materials and any complications, the price can be even greater. DIY stair hardwood installation are often more expensive because you must acquire all the tools and materials yourself. The final cost can also depend on the woods you select and the particular shape of your stairs, whether you have an open stair case or closed stair cases. Open is when the staircase stringer comes right to the edge of the stairs, and closed are when the staircase stringer come above the side raisers. Open staircases are more expensive to install and can be around $200.00 per step, and closed will be $120.00 to $150.00 per step, depending on the width, standard is 36", with wider staircases being more expensive.
- Waste and Garbage Removal: Any flooring project has some waste and garbage that needs removal, and it is essential to do it legally and safely. If you have an older floor to remove, waste disposal can be a big project that requires a truck. Most contractors will offer this service as part of their installation costs. The cost of removing waste is usually $0.25 square foot for removing old floors and removing waste from newly installed hardwood floors. Depending on the contractor's particular overhead (e.g. how much they pay to their employees) the price can go up to $0.50 square foot.
- Designed Floors: Design price estimates can be done in two ways: Simple and complicated. If you choose to go with relatively standard floors patterns, which can be found on pinterest and other online idea sources, then design can be considered as included in the price. However, if you choose to go with more complicated wood types and patterns, then the work of a professional designer might be needed. If the design is a straight planks installation (basic installation), then the additional cost of design is usually zero, with installation costing around $3.00 per square foot. If the installation is in an angle with additions, or any other complication, then the price is customized to your job and can be negotiated with contractors only. If you want a particular design, then present photos of it to your contractor to get quote. Prices can go up as far as $150.00 per square foot for exotic designs.
- Hardwood Floor Material and Supply Cost: By now you already know that installing hardwood floors is not a simple task, involving a lot of equipment and materials in the preparation, installation, and finishing of the hardwood floors. The cost of all those additions is, on average, $1.75 per square foot. A few examples of the equipment you may have to pay for include gloves, goggles, or boots. Sullies costs are different from hardwood floor equipment cost in that the cover more advanced items like toxicity level measurement instruments or large scale polishing machines. There are many more items involved, such as supplies and tools like staple gun, glue, jars, knee pads, meters, etc. You can either choose to rent, purchase, or close an overall deal with a contractor for the needed equipment and materials. Some contractors charge delivery costs for hardwood floor materials and supplies, which is categorized as extra labor and charges usually reaching around $1.00 per square foot. For example, if you have all materials already stored in a separate location than that of your project, then the contractor might need to spend time or hire additional assistants to move the materials from the storage area to the working area, forcing them to charge extra.
- Moldings Costs: Hardwood molding, or base molding, are the costs of installing the trip of the hardwood floor where it meets the wall, staircase, kitchen, or other objects in the house. The price depends on several factors, like the type of wood selected for the molding (usually it matches the selected hardwood for the floor), the size of the floor, the length of the moldings, and the overall time needed for the installation, including all detail work that needs to be done. Costs can include the preparation and removal of materials, as well as the sophistication required of the particular project. If you´re considering a DIY project, major factors would be the need for tools for installation and finishing of the molding. If you´re not doing a DIY project, then the overall molding installation cost can vary from $5.00 to $10.00 per feet. You can control the cost of moldings and save money by choosing cheaper moldings.
- What Should or Can Be Excluded from Labor Costs and How Customers Can Save Money: First of all, you can save money by finding the right hardwood floor wood type for you at the right price. For example, purchasing the right level of strength so that you don´t pay more for strength you don´t need. If are able to install solid floors, then you might save on getting those versus the more expensive engineered hardwood floors. Secondly, if you can do the finishing yourself, then you can purchase unfinished hardwood floors and save money. Anything you can safely and effectively do yourself will save you cash: Moving furniture, removing existing floor, purchasing the materials yourself, etc. Ask yourself what you can do yourself and what you might need help with, such as electrical or plumbing work. Are there heavy items to move and can you do it yourself without damaging the house or new hardwood floor? Again, anything you can do yourself safely will save you money. However, in some cases, nice and generous contractors might offer to do all those things for free. Those type of things can sometimes be arranged online, and you can get great prices without even having a contractor come to your house. Lastly, you can choose to do the entire project as a DIY, saving money on labor and material costs.
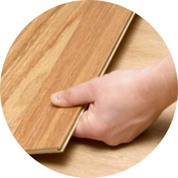
To DIY or Not to DIY
DIY remains an option for many skilled homeowners, with distinct advantages and disadvantages. The pro´s and con´s of DIY include:
- Lower Price: A DIY project, although dependent on scale, is a cheaper alternative to using a regular contractor. The downside, however, is that there is no guarantee you´ll install your floors better than an expert would have, which can mean costly repairs and sometimes re-installations down the line.
- Schedule: DIY projects allows for working conditions that suit your time; no need to arrange schedule hiatuses for the sake of a contractor.
- Speed: Without a contractor, a home improvement project can be done at a quicker rate.
- Self-worth: A person feels elevated through his/her accomplishment of a home-related task.
- Construction Errors: More complicated projects require higher levels of expertise, which, if lacking, may degrade and/or destroy the area under construction. Knowledge of materials and techniques are crucial for big projects. Paying for mistakes can be quite costly. Contractors, on the other hand, retain the skill and planning necessary for complex projects.
- Environmental Problems: A DIY homeowner may be unaware of environmental practices/standards, resulting in pollution and, subsequently, fines. Dust emissions, for example, are a common problem for DIY projects. Such problems don´t exist for contractors since they can accommodate the procedures.
- Lack of Equipment: Many homeowners do not posses the tools, nor the wisdom of how to operate them. Contractors don´t face this issue.
- Lack of License/Documents: Some projects require building or construction licenses, a document many homeowners don´t have. A fine can follow any unlicensed undertakings. It´s also fair to note that DIY may, inadvertently, cross private property boundaries, landing one in legal trouble.
- Longevity: Although varying by the skillset of a DIY constructor, projects typically last longer with contractor remodeling. The downside is that the DIY project might take much more time compared to a professional contractor. Professional installers know how to work fast and with quality. The only way to save here is if you have plenty of free time and the skills to install new hard floors.
The disadvantages become apparent in large projects where the aforementioned factors are of utmost importance. From the two lists, a conclusion may be formed: DIY stands as a viable option for small projects; larger projects should be completed by professional contractors.
- Hardwood Floor Installation Cost Calculator
- Hardwood floor planks cost
- Prefinished vs. Unfinished Hardwood Floor
- Solid vs. Engineered Hardwood Floors
- Installation and Labor Cost
- Hardwood Floor Additional, Optional, and Behind the Scenes Costs
- Contractor hiring
Comments
Comments are disabled for this post